浅析风电机组液压系统泄油路故障原因及解决方案
近年来中国风电产业发展迅猛,从2003年底风电装机容量的50万千瓦,发展到2013年并网容量7700万千瓦,吊装容量超过9000万千瓦,由世界排名第十上升为世界第一的风电大国,也建立了规模最大的风电产业。面对如此庞大规模的装机数量,并网后的机组日常维护与定期检修工作成为运营商和整机厂商最为关注的问题,因为这两项工作是影响风电机组发电量的主要因素。风电机组的运行维护,主要是围绕如何预防和解决风电机组运行过程中遇到的故障展开的,根本目的是为了有效控制风电机组的运行维护成本,提升客户(风电场运营商)满意度和风电场运营效益。根据风能发展较早国家和地区的经验,在3年-5年的运行后,风电机组开始进入一个故障多发期,机械系统的关键部件如齿轮箱、液压系统、偏航系统等开始集中出现不同程度的问题,其中液压系统故障排在机械系统常见故障数量统计的第二位,可见液压系统故障对风电机组日常运行的严重危害。然而,液压系统由于具有单位体积小、重量轻、动态响应好、扭矩大、容易实现过载保护等优良的特性,在风电机组中被普遍采用。因此,有效解决液压系统故障对于降低风电机组的维护成本与提高发电量具有非常重要的意义。本文就风电机组液压系统的泄油路液压油逆向流动故障导致的损失和危害做了说明介绍;依据针对故障的现场勘察资料与数据,分析造成液压油逆向流动的成因;并介绍目前常见的两种泄油路设计的解决方案,最后根据现有方案的优缺点,进一步提出故障的优化解决方案。
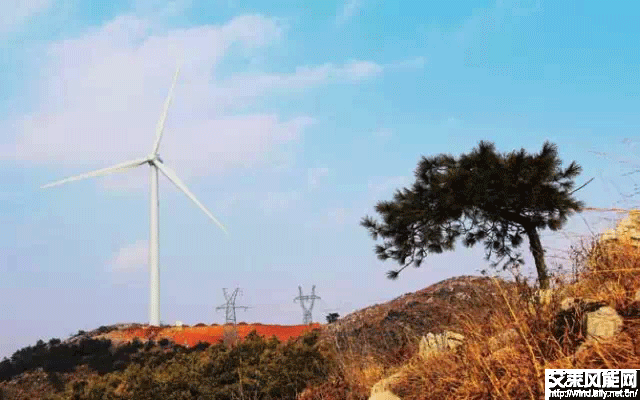
液压油逆向流动故障的危害
由于风电机组制动系统(主轴制动器与偏航制动器)中的驱动介质采用的是低粘度的液压油,同时制动系统的执行部件(活塞)在工作过程中不断运动,因而不可避免的存在油脂渗漏的问题。油脂渗漏一方面会导致液压系统的压力下降,无法满足风电机组的技术需求;另一方面渗漏的油脂会对机组内部造成污染,并对运维人员的工作带来安全隐患。为了解决活塞运动导致的液压油渗漏问题,制动器与液压系统生产厂家通常会在制动器和液压系统内部的液压回路中设置液压油的泄油回路,将渗漏出的液压油导向液压系统的油箱,如此既可以避免液压油渗漏造成的压力下降问题,又可以将渗漏的液压油回收再利用,具有环保高效的作用。其中液压系统的泄油回路连接结构如图一所示。
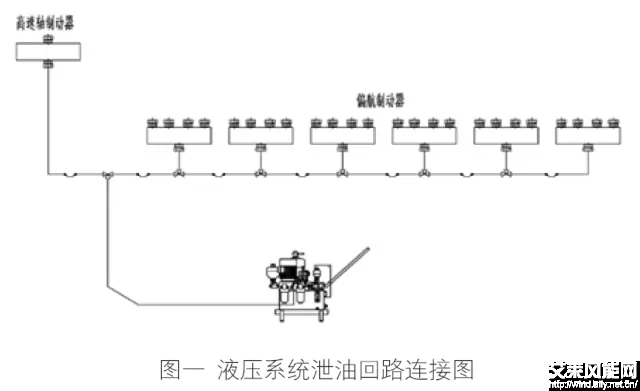
制动器的泄油回路结构是依据制动器内部的密封结构进行设计的。制动器内部的密封结构一般包含两道环绕活塞的橡胶密封圈,根据功能分为密封圈与防尘圈。密封圈位于靠近油缸底部的一侧(即远离摩擦片的一侧),可承受的压力较高,达到数十兆帕,确保制动器在制动状态的压力下液压油不致泄露;防尘圈位于远离油缸底部的一侧,可承受的压力相对较小,一般在5bar-10bar范围内,主要功能是防止制动器外部的各类杂质渗透到制动器内部,污染液压油。制动器的活塞在上下运动过程中会有液压油从油缸底部渗漏到密封圈与防尘圈之间,继而渗漏的液压油进入制动器泄油回路,然后被引导回油箱,重新回到液压系统的压力回路。一般风电机组液压系统的油箱位置比偏航制动器高2米-3米,即渗漏的液压油要积累到充满泄油回路的回油管后,方能进入油箱,因此防尘圈需能承受回油管中液压油造成的压力。偏航制动器的泄油回路如图二所示。

然而,实际运维工作发现本应被引导流回油箱的渗漏液压油,却意外自偏航制动器活塞中溢出。液压油自偏航制动器上侧活塞中溢出后,滴落在刹车盘上,对偏航摩擦副(摩擦片与刹车盘)的摩擦环境造成污染,导致偏航摩擦副的摩擦系数不再均匀一致,摩擦性能不再平稳,出现较大振动与噪声;摩擦片的摩擦材料由于采用了树脂基的复合材料,易受油脂侵入而变性,磨损率大幅上升,摩擦片的工作寿命快速下降,超出风电机组的定检维护周期,如果未及时发现就会导致刹车盘被摩擦片背板磨损的严重事故。偏航制动器摩擦片被油脂污染的情况如图三所示。
液压油逆向流动故障的原因分析
依据前一节所介绍的液压油泄油回路的工作原理可知,如果偏航制动器密封结构的密封圈失效,会造成液压油大量泄露,进而液压系统压力快速下降,而现场实际遇到的情况并未出现大量油脂泄露,系统压力也没有发生明显变化。因此,导致液压油渗漏的直接原因是防尘圈与密封圈之间的压力超出防尘圈的承受范围。防尘圈与密封圈之间的压力是由连接偏航制动器与油箱的回油管中的液压油导致的,该压力计算如式(1)。
P=tgh(1)
式中,ρ为液压油密度,800kg/m3;
g为重力加速度,9.85m/s2;
h为油箱与偏航制动器之间的高程差,按3m计。
由式(1)计算可得,液压油造成的压力为23640Pa,并且油箱应与大气连通,内部无负压,而防尘圈可承受的最小压力为50000Pa,所以理论上偏航制动器渗漏的液压油应回流到油箱中。
经过调查研究,分析得出导致泄油回路渗漏的可能原因包括以下三个方面:
(1)防尘圈失效;
(2)油箱内部存在负压;
(3)液压阀块上的泄油路通道与泄压油路连通。
经试验验证,原因(1)与实际情况不符,原因(2)的条件不成立。因此初步判定泄油回路渗漏的原因为阀块中的泄油路与泄压油路或其他存在压力的油路连通,使得泄油路末端出现额外压力,造成泄油回路的液压油渗漏。
针对故障的优化解决方案
针对风电机组液压系统泄油回路的设计问题,目前较为常见的方案有两种:回油管方案与集油瓶方案。图一所示的泄油回路使用的即是回油管方案,该方案的使用缺陷在第一节中已经进行了详细介绍,此处不再赘述。
集油瓶方案是指,将集油瓶直接连接到偏航制动器的泄油口上,集油瓶用于收集偏航制动器密封圈溢出的液压油,集油瓶的底部有与外部空气连通的呼吸口,确保液压油能够顺畅流入集油瓶。该方案目前在风电机组中也被普遍采用,其优势是结构简单、维护方便,有效避免液压油逆向流动等。但是实际工作过程中,该方案存在无法容纳大量液压油泄漏,导致风电机组内部严重污染的严重后果。
为了解决回油管方案液压油逆向流动的问题,并解决集油瓶方案的泄漏油液容纳能力不足的缺陷,需要对这两个方案进行优化改进,同时还需保留两方案现有的优点。经过反复试验研究,将现有两方案有机结合,已初步形成一个去芜存菁的优化方案。优化解决方案是保留回油管方案中的回油管路,将一种特制的集油瓶连接到与液压站泄油路接口连通的偏航制动器,特制集油瓶的端盖上除了常见的接口外,另外增加一个通过回油管与主轴制动器的回油管会合后,一起连接到液压站泄油路接口,如图四所示。
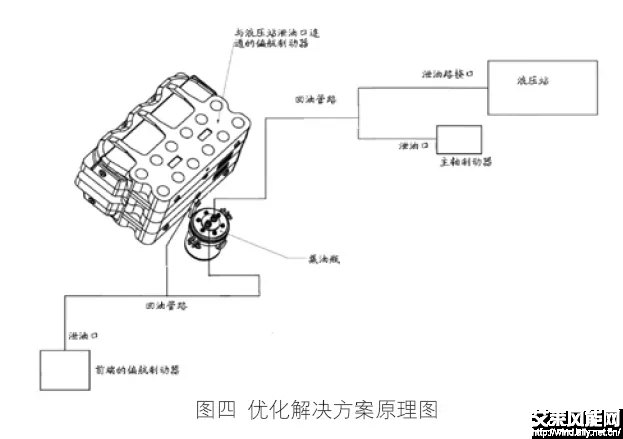
该方案既保留了回油管方案可将渗漏液压油回收再利用的节能环保优势,又将传统集油瓶方案的液压油容纳能力不足的弊端予以消除。该方案中特制集油瓶有一个与外界连通的呼吸口,确保瓶内压力与大气压相等,从而解决偏航制动器泄油口压力高于防尘圈压力上限导致的液压油泄漏问题。
结论
综上所述,面对风电机组日常维护过程中遇到的液压系统故障问题,为了确保机组的发电量与可利用率达标,并提升机组整体性能,必须从根本上解决维护过程中经常遇到的液压系统故障问题。本文以液压油的逆向流动问题为切入点,分析介绍了故障的严重危害与发生原因,并依据现有的泄油路解决方案,提炼出针对液压油逆向流动的初步解决方案。希望借此抛砖引玉,能够为风电机组液压系统工作性能的提升工作提供参考。